Sportswear: faster, better, greener?
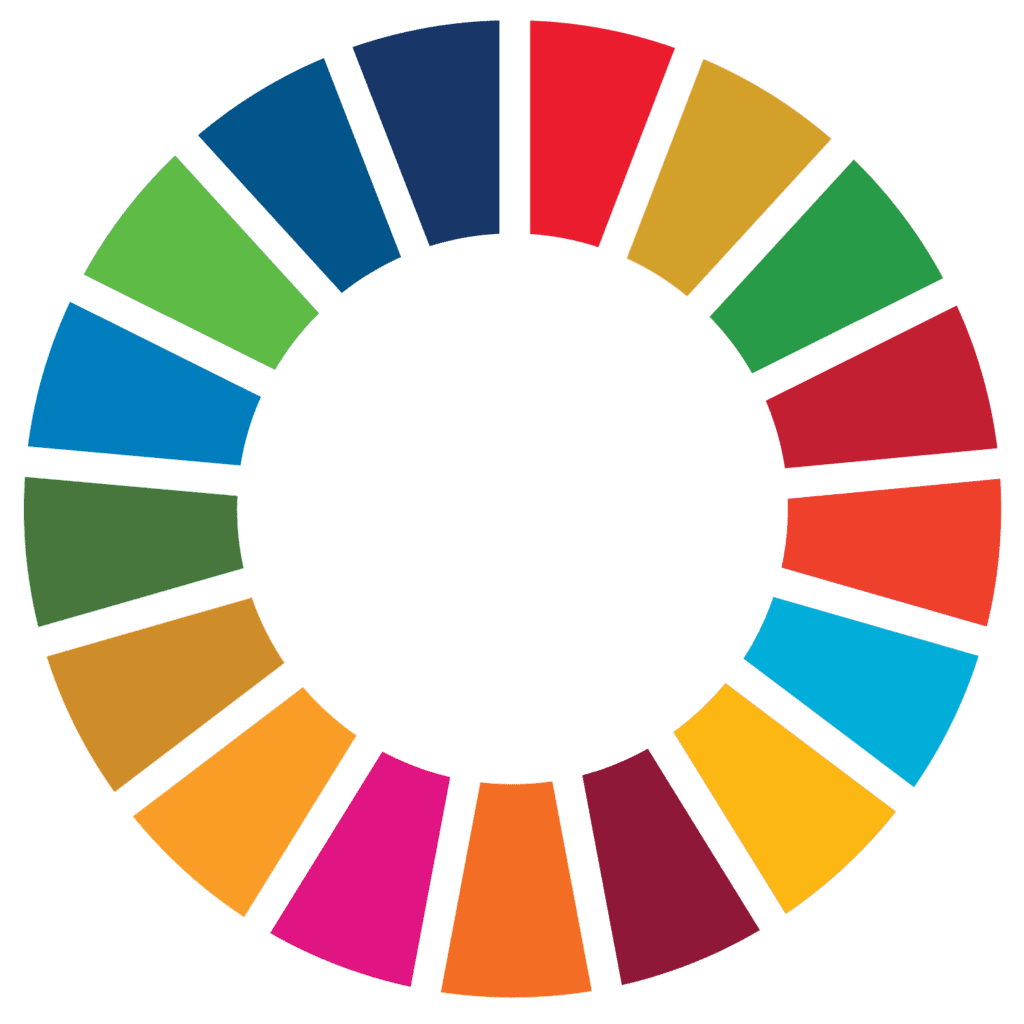
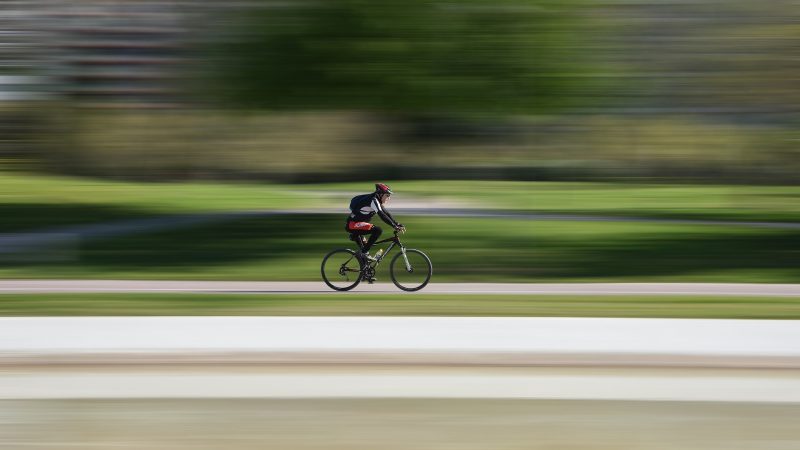
It is no secret that the textile industry has an enormous environmental impact on the world. When it comes to pollution, it is ranked second after the petroleum industry, and in terms of waste, every second a garbage truck of clothes is dumped into landfills. The sportswear industry comes with an extra environmental cost, as it is technologically and performance-driven and therefore uses petroleum-based textiles such as polyester and nylon.
The textile world is slowly becoming more sustainable, by using recycled materials in their finished products. Nevertheless, in a world where fast fashion and low-price products are ruling the market, a whole lot more is necessary to change the impact of the textile industry in a positive way.
Sustainability isn’t built in a day
Becoming sustainable is something that needs a lot of time and effort, but every bit helps. Bioracer is an example of a company that is wanting to change. They have been growing in the sportswear market, and they specialize in customized and high-performance cycling, ice skating, running, and triathlon clothing. Their mission is to make you faster, but the more pressing question now is if they can do it in a sustainable way.
Therefore, Anton Princen investigated the possibility of increasing the sustainability of their performance-driven sportswear in the different stages of their life cycle.
Pictures: Anton Princen
The original “Icon cycling line” from Bioracer formed the starting point of his research project and includes a cycling jersey and a bib short. When it comes to these products, not only looks are important, but the technical side of performance is key. The garments need to be developed to make you faster and more comfortable while riding the race bike. This presented an extra challenge because sustainable development cannot interfere with the performance of the garment.
In his research project, Anton developed two alternative lines to this “Icon cycling line” that are both more sustainable: the “Blue Ocean line” and the “Almost Zero Waste line”. The goal with these was to lower the environmental impact and assure the same performance and fit.
First, Princen wanted to investigate if the change to recycled materials lowered the carbon footprint and whether the quality and performance of the garment was maintained. He did this in the ‘Blue Ocean line’ by focusing on fabric material selection; he replaced all the virgin fabrics by a recycled variant.
To go even further, Anton also investigated the sustainable possibilities in the other phases of the life cycle with his ‘Almost Zero Waste (AZER0) line’. This includes material selection, cutting waste reduction, ink reduction and design for longevity and circularity.
However, sustainability in the whole life cycle is not easy to accomplish in the textile industry. Princen had to make a lot of changes in his two clothing lines.
Changing for the better
First of all, he switched to recycled fabrics, and made pattern changes in order to have no zipper and grippers to reduce weight and result in an almost completely recycled jersey. These pattern changes were also done to reduce the impact of the fabric cutting stage of the bib short. The reduction in the amount of cutting waste was achieved by optimizing the suspenders and main fabric of the bib short.
Furthermore, in order to reduce the amount of ink, Princen created a new pixelated dot design and implemented it in the Almost Zero Waste outfit. He also chose to stitch the seat pad together with a dissolvable yarn in order to prolong the lifetime by the implementation of an easy way to repair the bib short with a new seat pad.
The test: same quality, less waste?
When he made these changes, the next question that came up was if these alternative materials and processes are equal in quality to the old materials? To solve this question, he did some tests. The recycled fabrics and stitching threads are tested to check their performance by the tensile, stretch and fabric touch tester.
He also compared the recycled stitching threads with their virgin stitching threads in terms of tenacity and shows comparable results, so the quality is almost equal and could therefore easily be implemented in all of the jerseys and bib shorts without losing performance.
The fabrics are tested by a stretch tester and Fabric Touch Tester. The stretch test assures that the elongation of the recycled fabrics is within an acceptable range compared to the original fabrics. For the main fabrics, this is the case and for the other fabrics, it was tested whether they still fit with the different stretch, which was the case. Princen used The Fabric Touch Tester as a screening tool for thickness and thermal parameters since it was not possible to calculate the comfort parameters.
Picture: Fabricio Macedo FGMsp via Pixabay
To reduce the amount of cutting waste that often comes with producing clothes, Anton used The Marker Efficiency Analysis, which first determined the best overall parameters for the inlay process. He concluded that inlay of all sizes 0-10 together on a long table with a fabric width of 160cm gave the least amount of cutting waste. He used these settings to compare the overall cutting waste of the Original Icon bib short with the Almost Zero Waste bib short that has an optimized design to reduce this waste. This was successful since the amount of waste was 40% reduced.
The ink saving project succeeded in reducing the impact of the printing process, because by changing the print to a dense dot design it was possible to use 25% less ink. In reality, this print still shows some vertical and horizontal band formation, hence some improvement of the printer parameters is necessary.
The implementation of a dissolvable stitching thread for the seat pad is an improvement at the end of life stage of the product’s life cycle. Since it gives the possibility of removing the old seat pad and replacement by a brand new seat pad to prolong the lifetime. This was achievable by using a heat transfer press with an inflatable membrane.
Princen also thought of the phase after the production of the clothes: the distribution phase. He created a packaging alternative, since the clothing was initially distributed in a small unsustainable plastic protection bag. He replaced this by an implemented protection bag inside the jersey itself, so that the no plastic needed to be used anymore.
All good, but is it really more sustainable?
Lastly, the big question was if these changes were actually useful to increase the sustainability of the products. For this, Anton used a simplified life cycle assessment tool, named Bilan Produit. The tool is able to calculate the CO2 emissions and energy usage of the different products.
However, we need to keep in mind that it is calculated by a simplified LCA tool, which is therefore less accurate and reliable. But it is still able to locate the most impactful phase of the life cycle and it is a good tool to compare different alternatives to get a first impression of what the reduced impact would be.
He could conclude that The Blue Ocean line is potentially 30% better than the Icon Original line. The Almost Zero Waste jersey has even the potential to have a 40% decrease in CO2 emissions and energy usage. The Almost Zero Waste bib short has a reduced impact since the cutting waste is 40% less than the Icon Original and Blue Ocean bib shorts. Hence this eco-audit shows the potential of both alternatives to have a reduced impact on the environment.
Running towards a sustainable future
What Princen could draw from this project was that it succeeded in starting the sustainable development within Bioracer. He hopes that both of these sustainable lines will be implemented in the catalogue soon and all of the changes made in the different life stages (materials selection, pattern making, fabrics cutting, printing process and end-of-life) are improvements that could help the further development of Bioracer’s new quest for sustainability.