Hoe puzzelen met een 3D-printer elektromotoren efficiënter kan maken
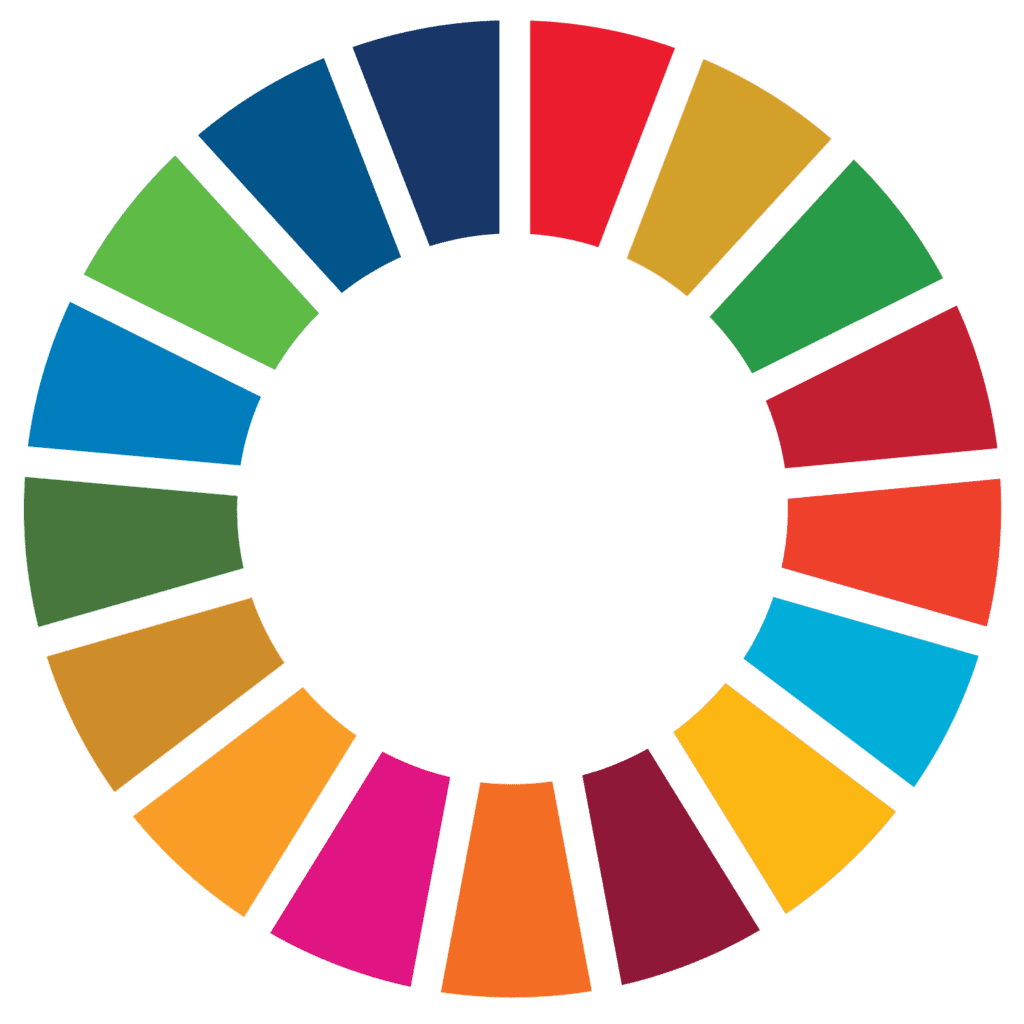
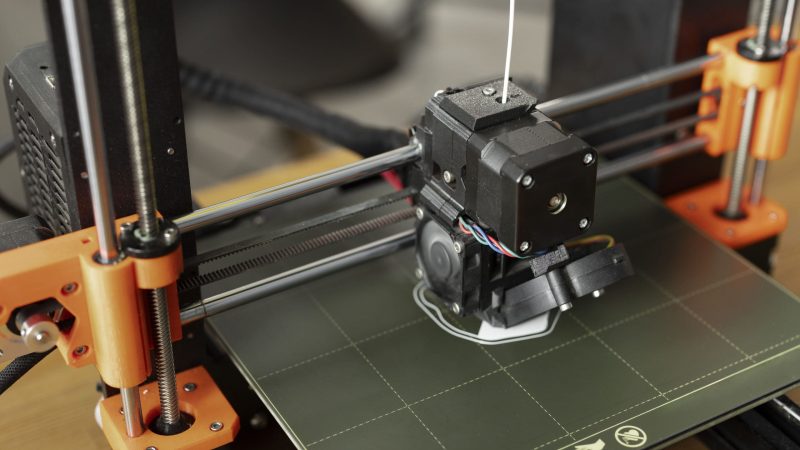
De puzzel tot magnetische precisie
Elektrische machineonderdelen voor motoren of transformatoren worden gemaakt uit ferromagnetische staalplaten, zoals siliciumijzer, om magnetische velden goed te geleiden, beter bekent als elektrisch staal. De efficiëntie hiervan hangt sterk af van hoe de ijzerkristallen in het metaal zijn georiënteerd. Net zoals je legoblokken moet oriënteren om een stevig bouwwerk te bouwen, willen we de kristallen zo rangschikken dat ze optimaal samenwerken.
Om je beter in te beelden hoe dit materiaal wordt opgebouwd, kun je je het Atomium voorstellen. Dit bouwwerk toont een kubusvormige eenheidscel van een ijzerkristal, waarbij de bollen ijzeratomen voorstellen. Wanneer meerdere eenheidscellen perfect gestapeld worden, vormen ze een monokristal. Alle objecten uit metaal zijn opgebouwd uit dergelijke grote ijzer monokristallen die samen een polykristal vormen, waarbij elk kristal een afzonderlijke oriëntatie inneemt.
Voorstelling van kristalstructuren, foto door Lukas Lammens
De kristaloriëntatie is belangrijk omdat ijzer magnetische anisotropie vertoont, wat betekent dat magnetische veldlijnen een voorkeursrichting hebben in het materiaal. In deze richting ervaren de veldlijnen het minste ‘weerstand’ en vereisen ze het minste energie. Magnetische verzadiging is het moment waarop al het materiaal is gemagnetiseerd. Dit kan worden bereikt bij verschillende energieniveaus, afhankelijk van de kristaloriëntatie. Voor efficiëntere machines zoeken we materialen waarvan de voorkeursrichting parallel loopt met de magnetische veldlijnen, wat het energieverbruik vermindert.
Zo zijn er twee soorten elektrische stalen: wel en niet-georiënteerd. Een wel georiënteerd staal bevat kristallen die grotendeels dezelfde oriëntatie hebben. Bij niet-georiënteerde stalen heerst voornamelijk een willekeurige kristaloriëntatie. Georiënteerde stalen worden dus gebruikt in machines waarbij de gewenste kristaloriëntatie altijd evenwijdig loopt met de magnetische veldlijnen.
Bouwblokken uit supermateriaal
Voor de bouwblokken van de machineonderdelen zal er gebruik worden gemaakt van ijzer met een hoog siliciumgehalte. Elektrische stalen bevatten doorgaans 3% silicium, maar de optimale legering bevat 6,5% silicium. Een hogere concentratie silicium verandert de elektrische eigenschappen en verbetert de efficiëntie van de machine. Helaas is deze legering niet geschikt voor het walsen in platen, voornamelijk door het brosse gedrag en de scheurvorming die optreedt tijdens plastische vervorming.
Om dit te vermijden gebruiken we een proces dat lijkt op het bouwen van een zandkasteel. We gebruiken harde korrels Fe6.5Si, die we in de gewenste vorm kunnen plaatsten zonder plastische vervorming. Een vereiste voor deze korrels is dat ze monokristallijn zijn, zodat de volledige kristalstructuur bepaald wordt door de oriëntatie van de korrel tijdens het plaatsen. Deze monokristallen hebben een gemiddelde diameter van 25 µm, wat resulteert in een fijn poeder.
3D-printmethode met poeder
Nu de bouwblokken bepaald zijn, kan het puzzelen starten. Dit is een combinatie van de twee onderdelen: 3D-printen met materiaal in poedervorm samen met het positioneren van de kristallen waarbij controle over de oriëntatie mogelijk is.
Het eerste onderdeel wordt opgelost door gebruik te maken van een bindmiddel, zoals water bij een zandkasteel. Dit onderzoek gebruikt een alcoholoplosbaar polymeer gemengd met het poeder, dit vormt een viskeuze pasta die via een spuitmond kan worden geëxtrudeerd. Na het 3D-printen verdampt de alcohol uit de pasta, waardoor het polymeer verhardt. Het verdampingsproces werkt als een lijm die de korrels op hun plaats houdt. Om het onderdeel nog te versterken, ondergaat het een thermische nabehandeling. Eerst verdampt het polymeer bij 500°C, waarna bij 1150°C de korrels samengroeien via een diffusieproces. Hierbij wisselen naburige korrels atomen uit, wat leidt tot een sterke atomaire verbinding. Dit zorgt voor stevige componenten, ideaal voor elektrische machines.
Magnetisch veld beïnvloede extrusie
Het tweede onderdeel berust op hetzelfde principe als een kompasnaald: net zoals de naald zich volgens het magnetische veld richt, zullen we de kristallen laten roteren. Om dit te bereiken, worden de kristallen eerst blootgesteld aan een sterk magnetisch veld van 1,6 Tesla, waardoor ze veranderen in kleine permanente magneten.
De elektromagneet die wordt gebruikt voor het magnetiseren van de kirstallen, foto door Lukas Lammens
Tijdens het 3D-printen creëren we een magnetisch veld rond de spuitmond. Hierdoor draaien de gemagnetiseerde ijzerkristallen vanzelf in de juiste richting, zodat de kristallen zich correct positioneren in de geëxtrudeerde pasta die het object vormt.
Schematische voorstelling van door een magnetisch veld beïnvloede extrusie, afbeelding door Lukas Lammens
Kristalrotatie in actie
Tijdens het onderzoek werden verschillende condities met elkaar vergeleken door proefstukken te extruderen. Zo werd de invloed van de spuitmondopening en het extern magnetisch veld onderzocht. De proefstukken werden getest via een EBSD (Electron Backscatter Diffraction) meting. Deze speciale meting straalt elektronen op een oppervlak van het proefstuk, en afhankelijk van de weerkaatsing van de elektronen kan de oriëntatie van de kristalstructuur worden bepaald. De meting onderzocht een gebied dat bestaat uit een honderdtal verschillende kristallen. Wanneer dit gebied grotendeels gelijkaardige kristaloriëntaties vertoont, hebben we het gewenste resultaat bereikt, en dus een georiënteerd elektrisch staal.
Uit de metingen bleek een grotere veldsterkte met een smallere spuitmonddiameter van 580 µm de beste resultaten te geven. Via statistische methoden werd gekeken welke oriëntatie het vaakst voorkomt, en zo kon een lichte intensiteit van de gewenste oriëntatie worden waargenomen. Dit betekent dat een beperkt aantal kristallen in de pasta zich roteerden in de juiste richting zoals kompasnaalden. Jammer genoeg is dit nog beperkt, een mogelijke oorzaak is het viskeuze gedrag van de pasta dat rotatie tegenwerkt.
Conclusie
In deze masterproef werd onderzocht of we georiënteerde materialen kunnen maken door 3D-printtechnieken te gebruiken. Door de korrels te magnetiseren en te mengen tot een pasta kunnen ze geëxtrudeerd worden in de gewenste vormen. Met behulp van een extern magnetisch veld wordt de rotatie van de korrels gerealiseerd. De eerste resultaten tonen verschijnselen van oriëntatie maar meer onderzoek is nodig naar de ideale set parameters. Deze nieuwe techniek kan leiden tot nieuwe concepten en ontwerpen voor het maken van efficiëntere machines die voorheen onmogelijk waren.